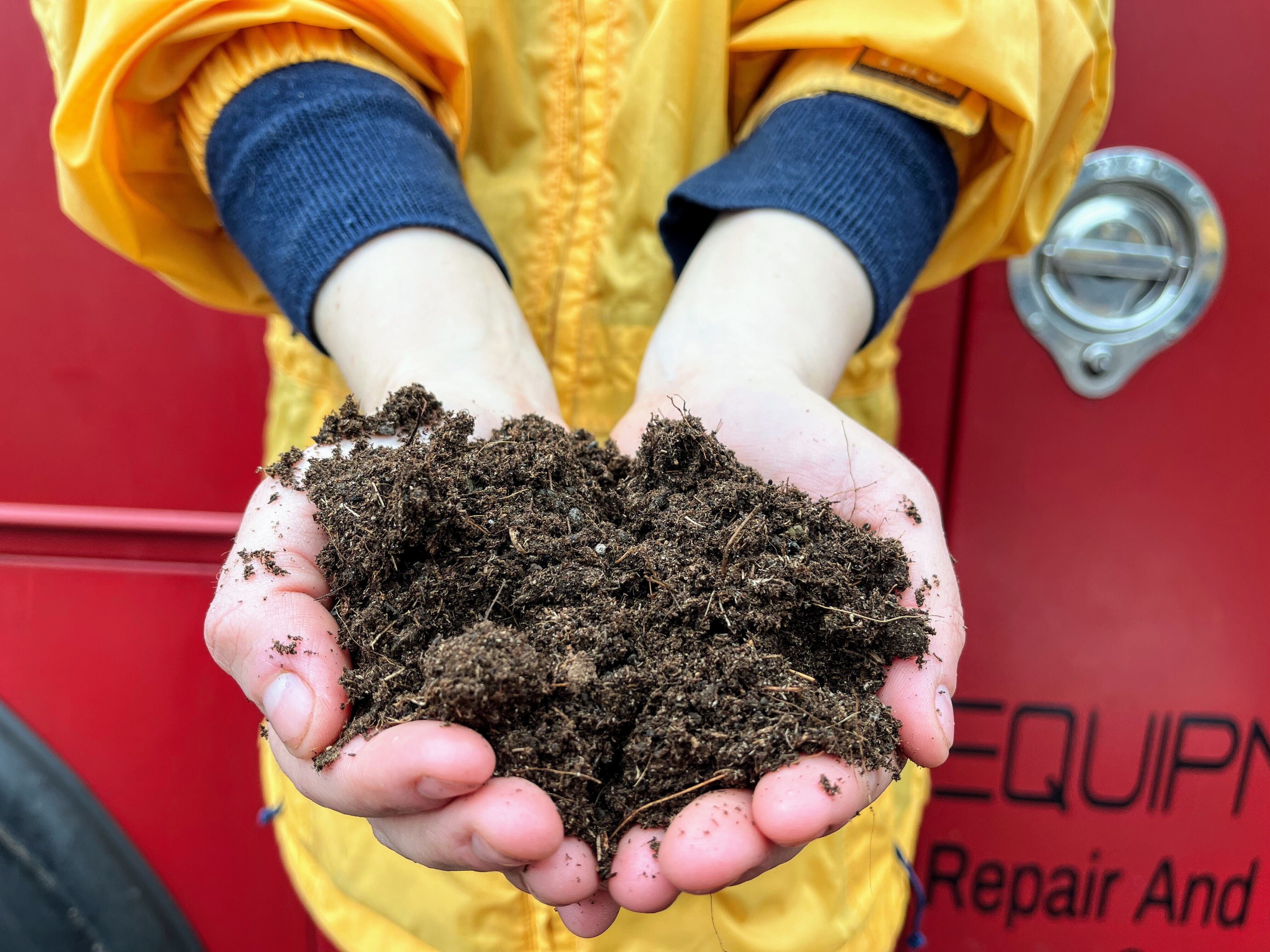
When crafting our potting soil blends, we consider seedlings’ initial needs in the greenhouse as well as the demands they will face after subsequent transplant into the field. Our potting soil is, essentially, a nursery in which young plants learn how to – among other things - search for water hidden in pore spaces, efficiently divide their roots in order to properly anchor themselves, and produce exudates that can be traded for nutrients under the management of soil microbes. For each of these processes, particle size impacts root responses.
Historical Development of Potting Soil
The first potting blends available on a commercial scale were developed in Britain, in the 1930s, by the John Innes Horticultural Institute; and were blended with a high percentage of loam soil (1). They were designed to replicate in a container the mechanics of a productive field tilth.
However, these blends compacted and behaved unsuitably when put through the rigors of cultivation in the relatively small volumes of potted culture. In addition, the material had to be harvested from turf, and demand began to outstrip supply, necessitating the development of loamless mixes (2).
These John Innes soils have a higher bulk density than most of the lightweight blends that have replaced them; sometimes, by as much as a factor of 10 (3). While these soils played an important role in the development of horticulture, they are nonetheless denser than a modern, properly mixed compost-based potting soil. This means that they are less forgiving of heavy-handed watering and, inversely, prone to desiccation when allowed to dry out substantially.
In an ideal field setting, a plant’s rhizosphere extends deep and wide enough to ensure water and air availability, even through cycles of saturation and aridity. However, in order to support the robust root growth that prepares seedlings for these conditions, a germination mix must be able to hold water without becoming anaerobic, and must also be able to dry evenly without ossifying.
Particle Size, Bulk Density, and Soil Handling Characteristics
While acceptable bulk density ratios may differ between field soils and container blends, they are, in both instances, the common structural determinant of healthy root growth (4). Optimal bulk density, therefore, is the sine qua non for all of our recipes, and we ensure it by allowing our soils to include a reasonable fraction of coarse particles.
These particles come from a variety of the components we use to blend our mixes, including peat (e.g. thin sticks with small protuberances), coconut coir (e.g. matted husk fragments), vermiculite, perlite, compost, and mineral amendments. Our goal is to produce blends that contain the ideal proportion of sizing gradations, and we must tolerate a small quantity of fragments on the upper limit of this range in order to prevent the soils from becoming too bulky.
Our Screening Process
Attempting to remove all particles larger than 12 mm, we first screen an incipient mix through a ¾” trommel. Once the blend is prepared with a suite of nutrients, it is screened again, this time through a ½” mesh.
In our experience, sizing reductions below ½” remove an excessive number of particles in the ideal 0.5-4 mm range, as smaller screen apertures are prone to plugging with soil, causing desirable-sized portions of a mix to cascade out and be lost. Additionally, if overdone, these screening sessions can break important structural amendments like perlite and vermiculite down into smaller sizes, thereby making the soil more prone to compaction (5).
After screening, our blends contain an acceptable spectrum of particle sizes, keeping with an industry standard that dictates threshold quantities of coarse and fine particles (6). However, outliers on the upper edge of this spectrum do occasionally make it through our screening process, despite our best efforts to exclude them.
Sphagnum peat, for instance, comes in a multitude of grades, but provides loft only when it contains a substantial unmilled portion. While peat itself has cavernous internal spaces (relative to the size of its particles), it is reduced to almost homogenous fines when milled, and the benefit of porosity is lost. Milled peat moss is widely available at hardware and garden stores, but is inferior to the grades that we source.
The coarser peat varieties found in our mixes do contain a visible quantity of small twigs, and a small percentage of these twigs inevitably migrate through our screens. While this may present an inconvenience, it is also proof positive that we are using the highest quality peat available.
Inclusion of Limestone
Once a soil blend has been screened, it is windrowed in our storage shed and turned periodically to ensure that it does not compress to such a degree that the growth of aerobic microbes is restricted. Were this repetitive process to take place on a concrete floor, the latter would eventually be compromised by the weight of our machinery; wearing unevenly, cracking, and, ultimately, fracturing into chunks and migrating into the potting soil. As such, we build the storage shed floors with limestone sized 3/8” and smaller, which accretes as water is added and compaction is applied to successive layers.
These floors are spot-fixed as needed and maintained by a full re-surfacing regimen every other year. We do expect a small amount of this limestone to loosen and incorporate into our blends. While these occasional bits of limestone exceed our ideal particle size, ultimately this inclusion is beneficial for the field in which our mix finds itself transplanted as a long-term contribution of calcium carbonate that serves to build soil structure.
Our Philosophy
While twigs and bits of limestone in our products occasionally make their way into our soils, we nonetheless stand by the intentionality of our sourcing and methods, and the high quality that these impart. As a part of our company ethic, we regularly trial new methods and materials, from trommels and peat to limestone of different sizes. However, we are confident that our current methods craft soil with a large enough particle size to encourage healthy root development, proper drainage, and living space for microorganisms, without causing significant interruptions to growers' workflow as they fill trays.
There are many potting media blends available to growers, but we remain confident that most growers recognize the divergence of profit-driven mass production from value-oriented craft, and - as an ethic - choose the latter. We are committed to this artisanal manufacturing process, and are grateful for the customers who, knowing its import, support our practices.
Sources
(1) Royal Horticultural Society, “John Innes potting compost”, https://www.rhs.org.uk/soil-composts-mulches/john-innes-compost
(2) A.C. Bunt, Media And Mixes For Container-Grown Plants: a manual on the preparation and use of growing media for pot plants, Second Edition, London, Unwin Hyman Ltd., 1988, pg. 2
(3) A.C. Bunt, Media And Mixes For Container-Grown Plants: a manual on the preparation and use of growing media for pot plants, Second Edition, London, Unwin Hyman Ltd., 1988, pg. 42
(4) USDA Natural Resources Conservation Service, “Soil Bulk Density/Moisture/Aeration”, pg. 3, https://www.nrcs.usda.gov/Internet/FSE_DOCUMENTS/nrcs142p2_053260.pdf
(5) George Kuepper, Kevin Everett & Luke Freeman, “Potting Mixes for Certified Organic Production”, ATTRA Sustainable Agriculture, 2004, rev. 2018, pg. 6, https://attra.ncat.org/htmlpub/potting-mixes-for-certified-organic-production/
(6) Raul Cabrera & Jim Johnson, “Fundamentals of Container Media Management, Pt. 1”, Rutgers University, 2014, https://njaes.rutgers.edu/fs812/